機械の転職 トップ > コラム一覧 > 日本の製造業を取り巻く環境で変わってきたTPM―全員参加の生産保全
2016年9月29日 木曜日配信 文 スタッフ-matsumoto
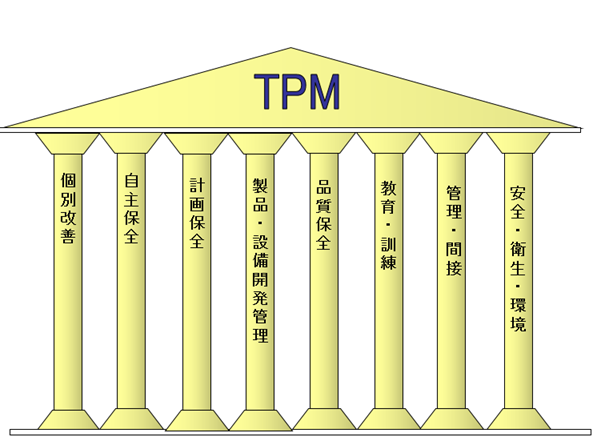
TPM(Total Productive Maintenance:全員参加の生産保全・全員参加の生産経営)は 40年以上の歴史を持つ、製造業企業の生産性向上のためのマネジメント手法です。
基本哲学は変わらずに、常に時代の声に応えて、新たな考えや手法を取り入れながら、全員参加の生産保全、生産経営と発展し続けてきました。
そして今、日本の製造業を取り巻く環境は、大きな変革を遂げようとしており、TPMも「変革的TPM」の時代に入ってきています。
■企業環境の4つの変化とTPMでの対応
製造業におけるグローバル競争は激しさを増しており、ますます強靭な企業体質の確立が必要とされている状況のなか、モノづくりに関わるあらゆる「ロス」の「ゼロ化」を目指すTPMの基本的手法が、極めて有効な手法として再注目されています。
「ロス」はあるべき姿と現状の差で、レベルが向上すれば新たな「ロス」を見つけ出し、この活動を継続することが強い競争力の源となります。
技術や技能を伝承する観点からも、IoT時代に先駆けて新たな技術を身に着ける観点からも、人の付加価値を高めようとするTPMは有効な活動手法です。
設備の高経年化や高機能化という問題に対しても、予防哲学から発展したTPMは、3,000件を超える国内外の企業・工場の経験に裏打ちされた具体的な各種分析手法が豊富にそろっています。
近年では、設備のライフサイクル全体を見渡したコスト管理が重要視されるようになり、企業トップの方針と現場の管理指標や活動指標のベクトル合わせを活動要件としてきたTPMの考えは、わかりやすい手法として活用されています。
企業の持続可能性という点についても、安全、衛生、環境保全を活動柱の一つとし、人間性の尊重を最も大事な哲学としてきたTPMの方向性が改めて重要視されています。
■TPMはどのように発展してきたのか?
「予防保全」という考えが最初に導入されたのは、1951年の東亜燃料工業(現、東燃ゼネラル石油)の活動からでした。その後、多くの企業がこの考えを積極的に取り入れ、1971年の日本電装(現、デンソー)の活動で、「全員参加の生産保全」のTPMが誕生しました。
そして、1982年にアイシン精機の活動で、「全社・全部門を対象とする」TPMへと発展していきました。さらに21世紀のTPMとして、「革新的」TPMに進化しています。
TPMのグローバル展開も加速され、現在までにTPM賞(TPM活動により成果を上げた事業場を表彰する制度)を受賞した企業や工場の約半数は海外となっています。
このようにTPM活動の方向性は、工場の活動から全社的な活動となり、さらにはビジネス全体を見渡した活動へと発展してきました。
主要経営指標(KMI:Key Management Indicators)、主要業績評価指標(KPI:Key Performance Indicators)、重要活動指標(KAI:Key Activity Indicators)を明確にすることで、成果と活動の関連性が、トップから現場までわかりやすいものとなっています。
■日本でのTPM活動への期待
日本におけるTPMへの期待は、大きく2つあります。
一つは人材育成、もう一つはトヨタ生産方式導入の前提としての役割です。
まず1つ目の人材育成について、最近、日本のモノづくり企業では、再度人材育成を強化し、失われつつある現場力を再構築しようとする動きが強まっています。
人材育成・確保に関しては、熟練者の大量退職などに伴う人材不足が極めて深刻であり、技術や技能の伝承に支障をきたす状況になっています。
人材育成を懸念する理由としては、分析力・論理的思考力不足、絶対的な経験不足、改善力不足などがあります。
また、海外生産における課題としては、現地リーダー資質、人材定着率、ワーカー資質などがあげられます。
このような課題に対し、もう一度現場力を再構築していく必要があり、TPMが見直されています。
2点目は、リーン生産方式(トヨタ生産方式)導入の前提に対する期待であり、TPMを再確認する動きがあります。
多くの企業がトヨタ生産方式の導入を進めてきましたが、真の意味でリーン生産体制を実現するためには、まずTPM活動をしっかりする必要があり、そうでないと、効果が低くなることが再認識されました。
あらためてTPMの視点からやり直そうという会社が多くなってきています。
■世界におけるTPM活動への期待
世界におけるTPMへの期待は、大きく3つあります。
まず、基本的にどこの国や地域の企業でも、実績のある優れた活動を取り入れたいという要請があります。
そして、海外に進出した日本企業や、地元の企業の活動を見たり聞いたりして、よい点を積極的に学びたいということで導入する例が多く、最も一般的です。
2点目は、グローバル企業が、世界の工場を統一した視点で管理するための手法としてです。
KMI/KPI/KAIの指標を工場ごとに比較でき、同じ視点で評価することができるため、食品業界のように世界各国に工場を展開する企業での活用例が多くなっています。
3点目は、企業文化の改革やモチベーション向上への期待です。
モチベーションをいかに上げていくかは、洋の東西を問わず共通の悩みです。
そんななか、日本の生産現場のモチベーションアップの施策となっているのが、「からくり改善」といわれる活動です。
現場主体で、お金をかけず、自分たちの作業が楽になり、効率化、低コスト化などにもつながる活動で、その工夫を設備設計にも生かそうとする動きがあります。
最近では、「からくり改善」が海外からも大きな注目を浴びています。
数多くの海外のTPM賞受賞企業が、独自の「からくり改善」を紹介するようになりました。
■TPM導入の意義と効果
継続的に成果を上げている事業場には、3つの特色があるといわれています。
指標とKMI、KPI、KAIの関連性が明確であること、企画から生産、販売までが一体となった活動を展開していること、ロスを徹底的に排除し、利益を向上させようとしていることの3つです。
そして、TPM活動の一番の意義は、多くの部門や人の仕事の質が上がることです。
TPM活動を導入、継続することで、人に力が付き、事後処理やモグラたたきのような非生産的な対応が減り、より先を見越した価値のある活動に取り組む文化を定着させることができるのです。
■設備保全の新しい流れ―ICTによる技術革新
今、生産性向上活動や設備保全の分野では、2つの動きがあります。
1つ目は、IoT(Internet of Things:モノのインターネット化)や人工知能(AI)を使った技術革新、2つ目は国際規格化です。
独のインダストリー4.0や、米GEのインダストリアル・インターネットの中核技術として、サイバー・フィジカル・システム(Cyber Physical System)が注目されています。
簡単にいうと、機械や部品などの物理的な(Physical)世界と、計算やシミュレーション主体の仮想(Cyber)の世界を接合したシステムです。
製造に関するデータを収集して解析し、故障診断や予測、予兆検知を統計的行う試みが進んでいます。
また、人工知能(AI)を使った取り組みも見られます。
ディープラーニング(深層学習)が得意な人工知能を使い、メンテナンスの熟練者のスキルを置き換えることができるようになるかもしれません。
これからの保全には、このような技術を自ら使いこなすか、データサイエンティストと呼ばれるような人と協力することも必要になるでしょう。
このような新しい流れの中で、サイバー・フィジカル・システムも人工知能も、道具でしかないということを念頭におかなければならないでしょう。
生産性向上や設備保全に取り組む担当者は、どのような課題が想定されるのか、どのような道具が使えるのかを考えながら、腕を磨いていくことが大切です。
2016年9月29日 木曜日配信 文 スタッフ-matsumoto
日本の製造業を取り巻く環境で変わってきたTPM―全員参加の生産保全
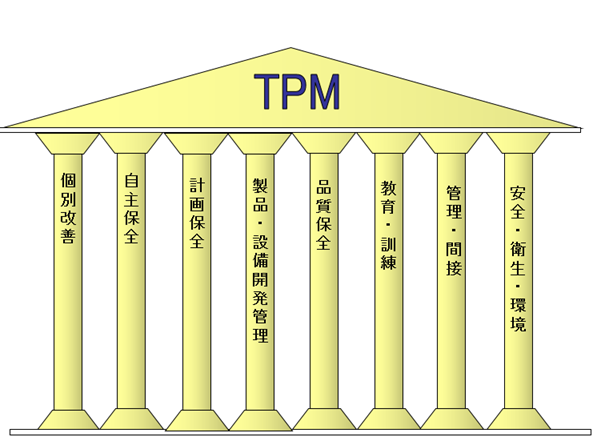
TPM(Total Productive Maintenance:全員参加の生産保全・全員参加の生産経営)は 40年以上の歴史を持つ、製造業企業の生産性向上のためのマネジメント手法です。
基本哲学は変わらずに、常に時代の声に応えて、新たな考えや手法を取り入れながら、全員参加の生産保全、生産経営と発展し続けてきました。
そして今、日本の製造業を取り巻く環境は、大きな変革を遂げようとしており、TPMも「変革的TPM」の時代に入ってきています。
■企業環境の4つの変化とTPMでの対応
製造業におけるグローバル競争は激しさを増しており、ますます強靭な企業体質の確立が必要とされている状況のなか、モノづくりに関わるあらゆる「ロス」の「ゼロ化」を目指すTPMの基本的手法が、極めて有効な手法として再注目されています。
「ロス」はあるべき姿と現状の差で、レベルが向上すれば新たな「ロス」を見つけ出し、この活動を継続することが強い競争力の源となります。
技術や技能を伝承する観点からも、IoT時代に先駆けて新たな技術を身に着ける観点からも、人の付加価値を高めようとするTPMは有効な活動手法です。
設備の高経年化や高機能化という問題に対しても、予防哲学から発展したTPMは、3,000件を超える国内外の企業・工場の経験に裏打ちされた具体的な各種分析手法が豊富にそろっています。
近年では、設備のライフサイクル全体を見渡したコスト管理が重要視されるようになり、企業トップの方針と現場の管理指標や活動指標のベクトル合わせを活動要件としてきたTPMの考えは、わかりやすい手法として活用されています。
企業の持続可能性という点についても、安全、衛生、環境保全を活動柱の一つとし、人間性の尊重を最も大事な哲学としてきたTPMの方向性が改めて重要視されています。
■TPMはどのように発展してきたのか?
「予防保全」という考えが最初に導入されたのは、1951年の東亜燃料工業(現、東燃ゼネラル石油)の活動からでした。その後、多くの企業がこの考えを積極的に取り入れ、1971年の日本電装(現、デンソー)の活動で、「全員参加の生産保全」のTPMが誕生しました。
そして、1982年にアイシン精機の活動で、「全社・全部門を対象とする」TPMへと発展していきました。さらに21世紀のTPMとして、「革新的」TPMに進化しています。
TPMのグローバル展開も加速され、現在までにTPM賞(TPM活動により成果を上げた事業場を表彰する制度)を受賞した企業や工場の約半数は海外となっています。
このようにTPM活動の方向性は、工場の活動から全社的な活動となり、さらにはビジネス全体を見渡した活動へと発展してきました。
主要経営指標(KMI:Key Management Indicators)、主要業績評価指標(KPI:Key Performance Indicators)、重要活動指標(KAI:Key Activity Indicators)を明確にすることで、成果と活動の関連性が、トップから現場までわかりやすいものとなっています。
■日本でのTPM活動への期待
日本におけるTPMへの期待は、大きく2つあります。
一つは人材育成、もう一つはトヨタ生産方式導入の前提としての役割です。
まず1つ目の人材育成について、最近、日本のモノづくり企業では、再度人材育成を強化し、失われつつある現場力を再構築しようとする動きが強まっています。
人材育成・確保に関しては、熟練者の大量退職などに伴う人材不足が極めて深刻であり、技術や技能の伝承に支障をきたす状況になっています。
人材育成を懸念する理由としては、分析力・論理的思考力不足、絶対的な経験不足、改善力不足などがあります。
また、海外生産における課題としては、現地リーダー資質、人材定着率、ワーカー資質などがあげられます。
このような課題に対し、もう一度現場力を再構築していく必要があり、TPMが見直されています。
2点目は、リーン生産方式(トヨタ生産方式)導入の前提に対する期待であり、TPMを再確認する動きがあります。
多くの企業がトヨタ生産方式の導入を進めてきましたが、真の意味でリーン生産体制を実現するためには、まずTPM活動をしっかりする必要があり、そうでないと、効果が低くなることが再認識されました。
あらためてTPMの視点からやり直そうという会社が多くなってきています。
■世界におけるTPM活動への期待
世界におけるTPMへの期待は、大きく3つあります。
まず、基本的にどこの国や地域の企業でも、実績のある優れた活動を取り入れたいという要請があります。
そして、海外に進出した日本企業や、地元の企業の活動を見たり聞いたりして、よい点を積極的に学びたいということで導入する例が多く、最も一般的です。
2点目は、グローバル企業が、世界の工場を統一した視点で管理するための手法としてです。
KMI/KPI/KAIの指標を工場ごとに比較でき、同じ視点で評価することができるため、食品業界のように世界各国に工場を展開する企業での活用例が多くなっています。
3点目は、企業文化の改革やモチベーション向上への期待です。
モチベーションをいかに上げていくかは、洋の東西を問わず共通の悩みです。
そんななか、日本の生産現場のモチベーションアップの施策となっているのが、「からくり改善」といわれる活動です。
現場主体で、お金をかけず、自分たちの作業が楽になり、効率化、低コスト化などにもつながる活動で、その工夫を設備設計にも生かそうとする動きがあります。
最近では、「からくり改善」が海外からも大きな注目を浴びています。
数多くの海外のTPM賞受賞企業が、独自の「からくり改善」を紹介するようになりました。
■TPM導入の意義と効果
継続的に成果を上げている事業場には、3つの特色があるといわれています。
指標とKMI、KPI、KAIの関連性が明確であること、企画から生産、販売までが一体となった活動を展開していること、ロスを徹底的に排除し、利益を向上させようとしていることの3つです。
そして、TPM活動の一番の意義は、多くの部門や人の仕事の質が上がることです。
TPM活動を導入、継続することで、人に力が付き、事後処理やモグラたたきのような非生産的な対応が減り、より先を見越した価値のある活動に取り組む文化を定着させることができるのです。
■設備保全の新しい流れ―ICTによる技術革新
今、生産性向上活動や設備保全の分野では、2つの動きがあります。
1つ目は、IoT(Internet of Things:モノのインターネット化)や人工知能(AI)を使った技術革新、2つ目は国際規格化です。
独のインダストリー4.0や、米GEのインダストリアル・インターネットの中核技術として、サイバー・フィジカル・システム(Cyber Physical System)が注目されています。
簡単にいうと、機械や部品などの物理的な(Physical)世界と、計算やシミュレーション主体の仮想(Cyber)の世界を接合したシステムです。
製造に関するデータを収集して解析し、故障診断や予測、予兆検知を統計的行う試みが進んでいます。
また、人工知能(AI)を使った取り組みも見られます。
ディープラーニング(深層学習)が得意な人工知能を使い、メンテナンスの熟練者のスキルを置き換えることができるようになるかもしれません。
これからの保全には、このような技術を自ら使いこなすか、データサイエンティストと呼ばれるような人と協力することも必要になるでしょう。
このような新しい流れの中で、サイバー・フィジカル・システムも人工知能も、道具でしかないということを念頭におかなければならないでしょう。
生産性向上や設備保全に取り組む担当者は、どのような課題が想定されるのか、どのような道具が使えるのかを考えながら、腕を磨いていくことが大切です。
【個人情報の取扱いについて】
当サイトより取得した個人情報は適切に管理致します。個人情報保護法に定める例外事項を除き、本人の同意を得ることなく第三者に提供、開示いたしません。
当サイトより取得した個人情報は適切に管理致します。個人情報保護法に定める例外事項を除き、本人の同意を得ることなく第三者に提供、開示いたしません。
TOP